PRODUCT PARAMETERS
Description
Introduction to Factory OEM customized heavy duty large module helical gear shaft helical shaft
Factory OEM customized heavy duty large module helical gear shaft helical shaft are important components in mechanical systems used to support rotating parts (such as gears, pulleys or sprockets) and transmit torque. They play a key role in mechanical equipment by connecting the power source with the working parts to ensure the effective transmission of power.
Characteristic advantages of Factory OEM customized heavy duty large module helical gear shaft helical shaft
High precision: adopting precision machining technology ensures the size and shape accuracy of the shaft and improves the transmission efficiency.
High strength: made of high-quality materials with good tensile, compressive and wear-resistant properties.
Reliability: After strict quality control, it ensures stable operation for a long time.
Versatile design: A variety of specifications and types are available to suit different applications.
Easy maintenance: the structure is designed for easy installation and repair, reducing maintenance costs.
(Factory OEM customized heavy duty large module helical gear shaft helical shaft)
Specification of Factory OEM customized heavy duty large module helical gear shaft helical shaft
This heavy-duty large module helical gear shaft is designed for industrial applications requiring high torque and precision. The product is built using top-grade alloy steel, ensuring strength and resistance to wear. Customization options allow for specific dimensions, tooth profiles, and surface treatments to meet unique operational demands. The gear shaft’s helical design provides smooth engagement, reducing noise and vibration during operation.
The manufacturing process includes advanced CNC machining and heat treatment techniques. These steps enhance durability and load-bearing capacity. Each gear undergoes rigorous quality checks to confirm dimensional accuracy and surface integrity. Tolerances are controlled within strict limits to ensure compatibility with existing systems.
Surface hardening methods like carburizing or induction hardening are applied to improve wear resistance. Corrosion-resistant coatings can be added for use in harsh environments. The helical teeth are precision-cut to optimize contact patterns, minimizing stress concentrations. This design increases service life even under continuous heavy loads.
The gear shaft supports high rotational speeds and bidirectional power transmission. It is suitable for industries such as mining, construction, and energy generation. Custom modifications include keyways, splines, or flange integrations based on machinery requirements. Material certifications and traceability are provided to meet industry standards.
Testing protocols include ultrasonic inspection for internal defects and hardness verification. Dynamic balancing ensures stable performance at varying speeds. Lubrication grooves can be incorporated to enhance maintenance efficiency. Technical drawings and 3D models are available for seamless integration into OEM systems.
Backed by engineering expertise, the product delivers reliability in extreme conditions. Production lead times are flexible to accommodate urgent orders. Technical support is provided to assist with installation and troubleshooting. Compliance with international specifications ensures global applicability.
(Factory OEM customized heavy duty large module helical gear shaft helical shaft)
Applications of Factory OEM customized heavy duty large module helical gear shaft helical shaft
Factory OEM customized heavy-duty large module helical gear shafts handle high torque and heavy loads in industrial settings. These components transfer motion between non-parallel axes smoothly. Their design reduces noise and vibration during operation. Industries rely on them for demanding applications requiring precision and durability.
Mining equipment uses these helical shafts in crushers and conveyors. The gears manage extreme stress from processing rocks and minerals. Their customized dimensions fit specific machinery layouts. This ensures efficient power transmission in confined spaces. Operators notice less downtime due to wear resistance from hardened materials.
Construction machinery integrates these shafts in cranes and excavators. The helical teeth distribute load evenly across the gear surface. This prevents sudden failures under variable forces. Customized modules match the speed and torque needs of hydraulic systems. Builders benefit from reliable performance in lifting and digging tasks.
Energy sectors install helical gear shafts in wind turbines and hydroelectric plants. The components handle fluctuating energy inputs without losing efficiency. Large modules support the slow rotation speeds of turbine blades. OEM customization aligns with generator specifications for maximum power output. Maintenance cycles extend due to robust construction.
Marine applications depend on these shafts for ship propulsion systems. Saltwater environments demand corrosion-resistant materials. Helical gears maintain alignment in turbulent conditions. Engine power transfers to propellers with minimal energy loss. Custom sizes accommodate engine room limitations.
Steel and cement plants use helical shafts in rolling mills and kilns. High temperatures and continuous operation test component reliability. Special alloys withstand thermal expansion. The helical design reduces shock during heavy material processing. Factories achieve consistent output with fewer breakdowns.
Precision manufacturing ensures each gear shaft meets exact client requirements. Engineers optimize tooth profiles for specific friction and load conditions. Advanced machining creates tight tolerances for seamless integration. Quality checks verify performance under simulated stresses. Clients receive components ready for immediate installation.
These helical gear shafts adapt to unique industrial challenges. Custom solutions address space constraints and operational demands. Industries prioritize them for critical systems needing longevity and precision. Performance improvements translate to higher productivity and cost savings.
Company Introduction
Established in 2002, Port of Machinery Co.,ltd. focus on metal research and mining machinery spare parts. 2 factories over an area of 13,300 square meters, based on 100+ sets of equipment, our production capacity reaches 12000 Tons/Year. has passed ISO 9001 quality managment system certification in 2008.
Our mainly products are dragline excavator spare parts,rotary kiln spare parts, large modulus gear (gear shaft), gearbox ect. 40+ patents with over 45 years experience to help focus on improve the service life of spare parts. We belive that more than 80% reason of mechanical parts’ working life depends on hot processing (steel making/forging/casting/welding/heat treatment). Eight material engineers will control the quality from the original resource.
If you are interested, please feel free to contact us.
Payment
L/C, T/T, Western Union, Paypal, Credit Card etc.
Shipment
By sea, by air, by express, as customers request.
5 FAQs of Factory OEM customized heavy duty large module helical gear shaft helical shaft
What customization options exist for heavy-duty helical gear shafts?
Custom helical gear shafts can be tailored to meet specific needs. Modifications include size adjustments, material choices, tooth profile designs, surface treatments, and load capacity enhancements. Clients provide technical drawings or specifications. The factory then engineers solutions matching exact performance requirements.
What materials are commonly used in these gear shafts?
High-strength steel alloys are standard. Carbon steel, alloy steel, and case-hardened steels are typical. Materials are selected based on application demands like torque, wear resistance, or environmental conditions. Heat treatment processes improve hardness and durability. Custom material requests are accepted for specialized projects.
How do helical gear shafts handle heavy loads?
Helical gears have angled teeth. This design spreads force across multiple teeth during operation. Stress distribution reduces wear and prevents sudden failure. Precision machining ensures tight tolerances. Heat treatments further boost strength. These factors combine to support high-load industrial applications reliably.
What quality checks ensure gear shaft reliability?
Every batch undergoes rigorous testing. Dimensional accuracy is verified with coordinate measuring machines. Surface hardness is tested using Rockwell or Brinell methods. Load capacity is validated through torque tests. Certifications like ISO 9001 guarantee consistent standards. Third-party inspections are available upon request.
What is the typical lead time for custom orders?
Lead times vary. Standard designs ship in 4-6 weeks. Complex custom projects may take 8-12 weeks. Factors include design complexity, material availability, and order volume. The factory provides timeline estimates after reviewing project details. Rush services are offered for urgent needs.
(Factory OEM customized heavy duty large module helical gear shaft helical shaft)
REQUEST A QUOTE
RELATED PRODUCTS
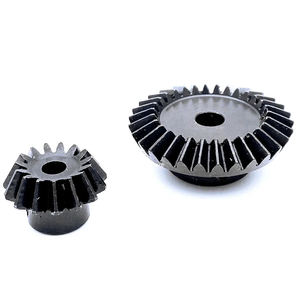
High Quality Whole Caliburn SUP Moulded Shaft And Flight Multiple Colors Accessories For Tungsten Darts Three Sizes
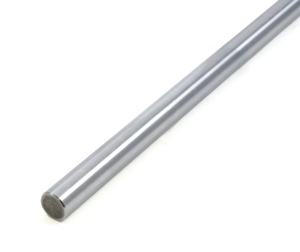
Spare Parts Komatsu 6D170-2 Rocker Arm Shaft 6162-43-5300
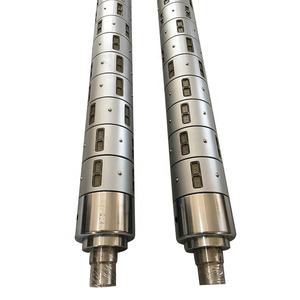
Screw Fasteners Motor shaft 410 420 Stainless Steel Screws Drive shafts For Juicer
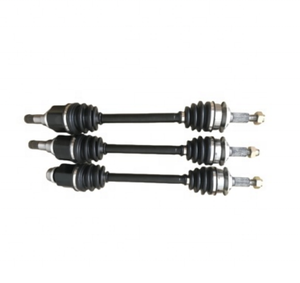
High Quality Carbon fiber shaft , Maple butt 58″ 4 color 1/2-pc Unilock Joint Billiard Pool Cue for
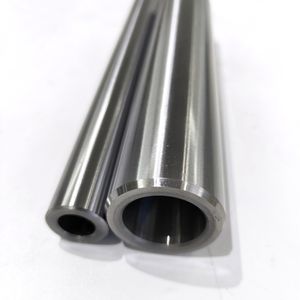
Low Stable Transmission Stable Structure Engine Camshaft Gear For Power Generation
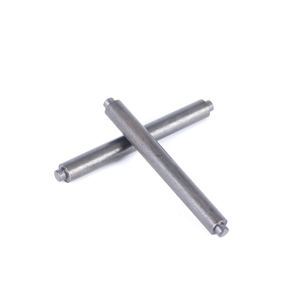